塑胶机械中的电磁感应加热技术 目前政府提倡全民节电, 共同行动。 而我国电力紧缺的省份, 据电监会发布的《电力供需形势分析及建议》 透露, 已达到 18 个。 全国各地累计拉闸限电超过 14 万条次, 累计限电量达 19 亿千瓦时, 电力紧缺已严重制约我国经济的发展。 因此, 政府大力扶持节能、 环保型产业。 据不完全统计, 全国现有塑料生产机械约 160 万台套, 每年还以 15%的速度递增,加热部分的电容量为 2000万千瓦,日用电量约为 2000万千瓦×0.5×20小时=2亿千瓦时, (0.5为机器加热通断比, 20 为机器一天生产的工时), 按每台机每年 300 个工作日计算, 全国塑料加工机械全年用电量为600亿千瓦时,若所有的机器都安装了电磁加热装置,那么全国节电约在180亿千瓦时,中比葛洲坝全年的发电量还多23亿千瓦时,对缓解国家电力紧张、降低国家投资和降低企业生产成本都有十分积极的作用和意义。
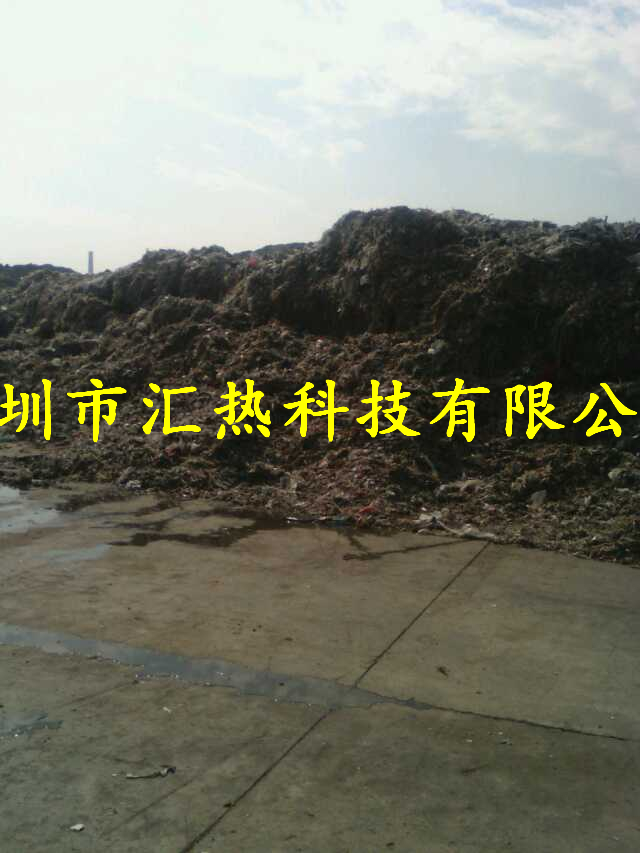
然而,随着世界经济的快速增长,能源及原料的供应出现短缺现象。塑料行业的能源消耗速度十分惊人,巨大的能耗不仅吃掉了塑料企业的部分利润,也使得当地的能源变得十分紧张。能耗,已经成了塑料行业发展路上的巨大“绊脚石”。塑料机械一直以来都有“用电大户之称”,近年来,随着制造业成本的增加,使得中国塑料制造业竞争日益激烈,节能已作为企业增效,降低经营成本,提高竞争力的重要手段,已经具有特别的意义,并逐步的被人们所认识和接受
国内塑胶行业现状及存在的问题
目前大部分塑料制品、塑料薄膜、塑料造粒、拉丝注塑、管材等生产企业的生产设备都是采用电热圈对料筒和模头进行加热,使塑料原料熔解塑化后再注模、拉伸,挤出成型为产品。存在以下问题:
1、热损失大:
现有企业采用的加热方式,是由电阻丝绕制的加热圈,加热圈的内外双面均发热,其内面(紧贴熔胶筒部分)的热传导到溶胶筒上,而外面的热量大部分散失到空气中,造成电能的浪费。
2、车间环境温度上升:
由于热量大量散失,周围环境温度升高,尤其是夏季对生产环境影响很大,现场工作温度甚至超过了45℃,有些企业不得不采用空调降低温度,这又造成能源的二次浪费。
3、传统发热圈使用寿命短、维修量大:
由于采用电阻丝发热,其加热温度长时间高达几百度温度,电阻丝容易因高温老化而烧断,常用电热圈使用寿命不长,因此,维修的工作量相对较大
4、由于车间内温度高,机器油温升高,大大缩短油封、油泵使用寿命,出现漏油和压力不稳定现象
1、大幅度节约电能 高频加热感应线圈和料筒之间加装一层隔热层,料筒内部的热量大部分被利用,只有微量辐射到空气中。料筒表面的温度一般在50-80度之间,经过严格的实验测试,节约电能在30%-80%,特别对于大功率注塑机节电效果更为明显;
2、明显降低车间的温度 通过以上的节能分析,使用高频加热系统不但是在设备节能上有改善,还改善了整个车间的温度,使员工在一个比较舒适的环境中工作;
3、加温迅速、温度控制准确 传统的电阻丝加热原理是电阻丝本身产生高温后热量再慢慢的从料筒外表传导到料筒的中心,速度缓慢,并且位于料筒中心的塑料实际温度和料筒表面温度有较大误差。而高频加热系统的工作原理是使金属料筒自身发热,热能是由料筒金属整体产生,温度控制实时准确,料筒内外温度一致,明显改善了产品的质量和提高了生产效率;
4、可以长时间在恶劣的环境中工作 ,塑胶机料筒的传统电阻丝在以下环境中使用降低它的寿命。如:加热位置遇到油污、料筒金属热传导不良、漏胶现象等。由于高频加热系统本身不发热,所以它不会把吸附在自身表面的油污、塑料颗粒等加热碳化,故不会产生漏电、短路等故障;
5、发热功率大,塑胶机料筒的传统电阻丝功率过大后对电阻丝本身的伤害加会加大,电阻丝金属本身在高温下会快速挥发,迅速老化而失效,所以传统电阻丝需要不定期的更换,而高频感应加热系统的特点是只有被感应的料筒金属内部才产生高温加热,自身电损耗小,所以功率大时也不影响高频加热系统的使用寿命,还可以根据自身需要来调节使用功率。
6、避免传统加热的不安全因素,使用高频加热系统后料筒表面的温度在50-80度以下,人体完全可以安全触摸;避免传统加热方式而造成的烧伤、烫伤事故的发生;